一种集成式电动车电池箱的制作方法
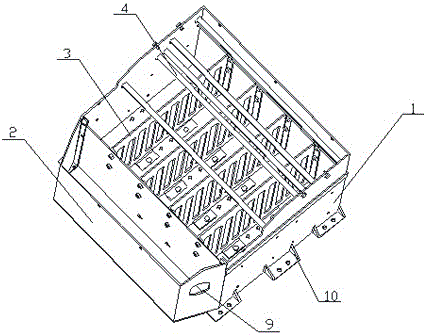
本实用新型属于电动车领域,具体涉及一种集成式电动车电池箱。
背景技术:
随着环境污染与能源危机的日益加剧,新能源汽车产业得到蓬勃发展,在此发展过程中,作为整车能量来源的动力电池系统成为电动汽车上最为关键的部分之一。然而由于电池的能量密度比传统燃油低很多,导致电池箱体积巨大,其质量占整车质量的比重也极大,同时电池自身在安全上的要求很高。这些因素对电池及其相关系统在车内的布置提出了挑战。
目前常用的布置方式中,比亚迪和特斯拉等采用将电池作为底盘的一部分平铺布置的方式,此外也有部分设计采用在座椅后方布置、在前舱和后舱分别布置的方式。在底盘布置时电池管理系统、充放控制电路等原件多布置于电池四周。虽然做到了集成,但整体平铺使面积过大,不利于拆卸。而其它布置方式中电池本身与管理系统等原件被分散于车上不同地方,同样不利于拆卸与系统调校。
技术实现要素:
为了解决上述技术问题,本实用新型提出了一种集成式电动车电池箱,该电池箱用于承载锂离子电池组、充放电回路和电池管理系统,同时,该电池箱还能够满足在实车上拆卸、维护方便等功能。
本实用新型的目的是这样实现的,该电池箱包括主箱体、前挂仓、内部隔板、支撑条、电池箱盖子、锂离子电池组、充放电回路和电池管理系统,所述前挂仓设置在主箱体的前面,四个内部隔板均布间隔设置在主箱体内部主箱体分隔成五个电池组放置空间,所述支撑条设置在主箱体内左侧围板和右侧围板之间电池组放置空间的上方,所述锂离子电池组电池组放置空间内,所述电池管理系统设置在支撑条的上面,所述充放电回路设置在前挂仓的内部,所述电池箱盖子设置在主箱体的最上方。
所述的主箱体由底板、前围板、右侧围板、后围板、和左侧围板连接构成,在右侧围板和左侧围板下端设置有多个加强肋板,在右侧围板、后围板和左侧围板上设置有侧围加强条。
本实用新型具有以下优点和积极效果:
1. 本实用新型通过设计一种集成式电动车电池箱,可实现锂离子电池组、充放电回路、电池管理系统的集成化设计,集成化程度高,有利于整车轻量化设计。
2. 本实用新型通过设计内部隔板,将主箱体分为5部分,能够有效防止电池组受侧向力时的左右晃动,减小电池组由于相互碰撞产生的冲击,保证电池组的安全。
3. 本实实用新型所述的前挂仓采用螺栓与主箱体前围板连接,将动力电池组与充放电回路有效隔开,易于拆卸,维修方便。
4. 本实用新型所述的支撑条可有效提高电池箱受侧向力时的刚度,同时,该支撑条布置于锂离子电池组上方,可将电池管理系统固定于支撑条上,减少线束长度,合理利用电池箱内部空间。
附图说明:
图1为本实用新型所述的一种集成式电动车电池箱的总装配图。
图2为本实用新型所述的一种集成式电动车电池箱的空箱体装配图。
图3为本实用新型所述的一种集成式电动车电池箱的主箱体轴测图。
图4为本实用新型所述的一种集成式电动车电池箱的内部隔板轴测图。
图5为本实用新型所述的一种集成式电动车电池箱的前挂仓轴测图。
图6为本实用新型所述的一种集成式电动车电池箱的支撑条轴测图。
图7为本实用新型所述的一种集成式电动车电池箱的盖子轴测图。
图中:1.主箱体,2.前挂仓,3.内部隔板,4.支撑条,6.锂离子电池组,7.充放电回路,8.电池管理系统,9.高压电出线口,10.加强肋板,11.底板,12.前围板,13.右侧围板,14.后围板,15.左侧围板,16.侧围加强条,17.内部隔板减重孔,18.内部隔板固定座,19.内部隔板固定通孔,20.前挂仓固定通孔,21.电池箱盖固定螺纹孔,22.电池管理系统从控盒固定螺纹孔,23.支撑条固定通孔,24.电池箱盖子固定通孔。
具体实施方式
为更好地理解本实用新型,下面结合具体实施方式对本实用新型创造做进一步详细阐述。目的是帮助本领域的技术人员对本实用新型的构思、技术方案有更完整、准确和深入的理解,并有助于其实施。
参阅图1、图2,一种集成式电动车电池箱,该电池箱包括主箱体1、前挂仓2、内部隔板3、支撑条4、电池箱盖子5、锂离子电池组6、充放电回路7和电池管理系统8,所述前挂仓2设置在主箱体1的前面,四个内部隔板3均布间隔设置在主箱体1内部主箱体1分隔成五个电池组放置空间,所述支撑条4设置在主箱体1内左侧围板15和右侧围板13之间电池组放置空间的上方,所述锂离子电池组6电池组放置空间内,所述电池管理系统8设置在支撑条4的上面,所述、充放电回路7设置在前挂仓2的内部,所述电池箱盖子5设置在主箱体1的最上方。
参阅图3,所述的主箱体1由底板11、前围板12、右侧围板13、后围板14、和左侧围板15连接构成,在右侧围板13和左侧围板15下端设置有多个加强肋板10,在右侧围板13、后围板14和左侧围板15上设置有侧围加强条16。
所述底板11采用4mm厚的5052铝板加工而成,锂离子电池组6通过螺栓固定在底板11上,在底板11左右两侧共有十二个直径为8mm的通孔,电池箱通过十二个8.8级M8的螺栓固定在电动车车架上。四块围板:前围板12、右侧围板13、主后围板14、左侧围板15均采用3mm厚的5052铝板焊接到底板11上,同时四块围板之间相互焊接,底板11与四块围板相互焊接后形成了主箱体1。为加强电池箱固定处强度,固定通孔处采用4mm厚的5052铝作为加强肋板10,加强肋板10分别与围板与底板11焊接。为加强侧围刚度,在右侧围板13、后围板14、左侧围板15上焊接一根侧围加强条16,该侧围加强条16由一根厚2mm,宽10mm的5052铝制成。
参阅图4,所述的内部隔板3由一块3mm厚的5052铝板弯折后加工而成,其中在内部隔板3上加工有减重孔17,侧面折边上带有内部隔板固定通孔19,所述内部隔板3下面设置有隔板底部固定座18,采用两个M6螺栓将底部固定座18与电池箱底板11连接,采用四个M6螺栓将内部隔板3分别与前围板12和后围板14连接,通过此种连接方式将四块内部隔板3固定在电池箱内部,将电池箱主箱体1分为五个部分,用于存放五组锂离子电池组6,能够有效防止电池组左右蹿动,防止相互挤压,以保护电池组安全。
参阅图5,所述的前挂仓2由一块3mm厚的5052铝板弯折后加工而成,其中在前挂仓2的侧面带有直径为6mm的前挂仓固定通孔20,所述前挂仓固定通孔20共计有四个,在前围板12上相对应的位置也有四个直径为6mm的通孔,采用四个M6螺栓将前挂仓2与前围板12连接起来。参阅图7,电池箱盖子5上有直径为6mm的电池箱盖子固定通孔24,共计六个,当前挂仓2与前围板12固定牢固之后,前部两个通孔与前挂仓2前部M4的螺纹孔采用M4的螺栓连接,电池箱盖子5前部可得到充分约束。在所述前挂仓2上还开有高压电出线口9,高压线通过此口引出。
参阅图6,所述的支撑条4由一根宽20mm,厚3mm的铝条弯折加工而成,其长度与电池箱内部宽度相同,其侧面有两个直径为6mm的支撑条固定通孔23,可根据电池管理系统的固定位置在电池箱主箱体侧面加工直径6mm的通孔,支撑条4采用M6的螺栓连接固定在电池箱内部。每个支撑条4上有八个M4的螺纹孔,参阅图1,两条平行的支撑条4上可平稳摆放电池管理系统从控盒,每个从控盒上有四个直径为4mm的通孔,采用四个M4的螺栓将从控盒与支撑条4上M4的螺纹孔连接固定,每两条支撑条4上可固定四个从控盒。
参阅图7,所述的电池箱盖子5由5052铝板弯折焊接而成,其形状及大小由电池箱主箱体1及前挂仓2决定,可灵活变换。电池箱盖子5上共有六个直径为6mm的电池箱盖子固定通孔24,分布在盖子的前部及两侧,前部两个通孔与前挂仓2上M6的螺纹孔采用M6的螺栓连接固定,侧面四个通孔与电池箱主箱体上M6的螺纹孔采用M6的螺栓连接固定。
技术研发人员:马芳武,代凯,蒲永锋,葛林鹤,安靖雅,刘宇朋,陈雪松
技术所有人:吉林大学
备 注:该技术已申请专利,仅供学习研究,如用于商业用途,请联系技术所有人。
声 明 :此信息收集于网络,如果你是此专利的发明人不想本网站收录此信息请联系我们,我们会在第一时间删除